Construction of the a typical through-hole aluminum electrolytic capacitor:
The vent is a crimp in the top of the aluminum can and comes in many versions, not just the X shown. The crimped metal is weakened so that if a failure in the capacitor causes gas to be generated, the crimp will crack and the gas will be vented. It's not found on all electrolytics and much rarer on SMD parts. The brownish disk helps reduce the amount of water lost to diffusion through the rubber "bung". "Drying out" is a common cause of failure. The capacitor can't be too well sealed however, small amounts of H2 and O2 are constantly being generated by electrolysis. The oxygen makes new aluminum oxide as required and the hydrogen diffuses through the bung.
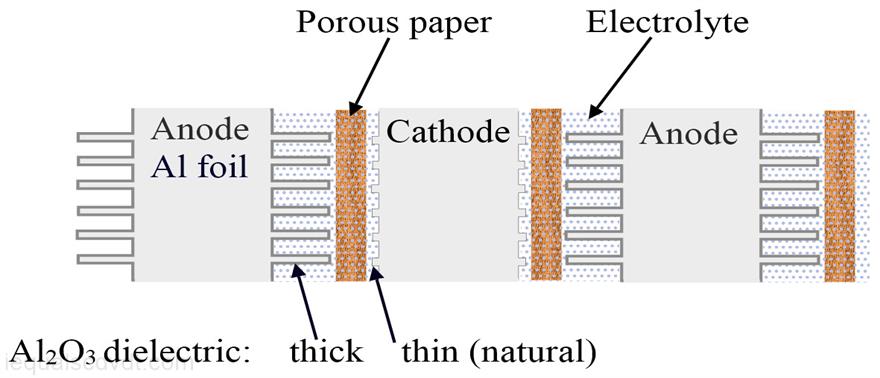
The picture below shows the construction of a classic liquid-electrolyte aluminum capacitor, overly stylized but you get the idea. The anode foil surface is etched to greatly increase the surface area, but will have different appearances depending on the capacitor's voltage rating. The picture below is typical of higher voltage capacitors. The cathode is also etched but the aluminum oxide coating is formed by natural exposure to air rather that grown electrolytically as it is on the anode. Technically, it's the electrolyte that is the cathode, a distinction few people make. The "cathode" foil just collects the electrons.
The paper is usually a high-purity cellulose type, but silk has been used in some exotic "audio" capacitors. Microporous polymer papers and even glass fabric have also been used. The paper is there to prevent direct contact between the two foils.
Below is a hybrid aluminum capacitor, part polymer electrolyte and part liquid. These are rare.