Written by Steve Elliott of Oren Elliott Products
Air-variable capacitors consist of two banks of intermeshed blades, one rotating, and the other stationary, supported by an electrically insulating framework. In use, opposite charges are placed across the two banks; adjustable blades of opposite charge are separated by an insulating air gap, which remains constant. Capacitance is varied by rotating the movable bank of blades, thus varying the degree of engagement of the two sections.
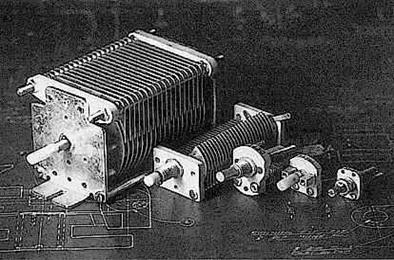
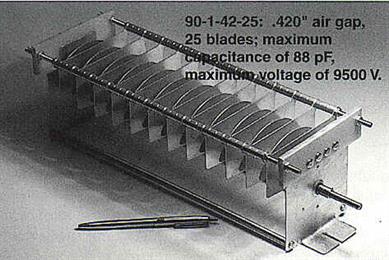
This is what would politely be called a very mature design, dating back to Marconi. However, it appears to be indispensable in many applications to this day; like copper wire Air1or ceramic insulators, its simplicity makes it a fundamental, timeless component. Most of these applications involve high frequency, high power, and low loss.
The classic application is Marconi's--short-wave radio tuning applications. Although most radio gear is now solid state, our capacitors still find their way into quite a few linear amplifiers and antenna tuners. This short-wave gear offers advantages of economy, durability, ease of maintenance, and nostalgia; it also lends itself to do-it-yourself modifications and experimentation by hobbyists
Our capacitors are still used in a few military radio-frequency applications, including missile guidance systems; admittedly, however, these are 1960's vintage systems, and the capacitors that we currently sell are used for spare or replacement parts. At the time, they were incorporated into the design partly because of their relative hardness to electromagnetic pulse (EMP), a burst of electrical energy created by a nuclear detonation that plays hell with modern circuitry. Today, experiments are being conducted to use a conventionally generated EMP in a weapon that can interrupt the function of a circuit; an example of its use by police would be to disrupt a fleeing car. This suggests possible future applications of air variable capacitors in EMP-hardened devices.
Currently, the primary application of air-variable capacitors is in advanced manufacturing processing machinery. Our capacitors are used in RF matching networks that control plasma used for a variety of advanced processes, including the deposition of conductive materials on silicon wafer substrates, and etching (removal of material or contaminants). These devices require high performance from the capacitors, and we've developed and refined our high-amperage electrical contact and our non-magnetic M73 primary for this application.
Another application that requires a non-magnetic capacitor is Magnetic Resonance Imaging (MRI) devices, the primary medical application of air-variable capacitors. Other applications have been under development, many involving the use of controlled plasmas as noninvasive surgical tools.
Instrumentation applications for air variable capacitors abound because of their remarkable stability over extended periods of time and under a wide range of conditions. One obvious application is in precision capacitance meters. Other applications involve testing the properties of the air (or other gasses or substances in which the capacitor is immersed) between the blades, like agricultural silo moisture meters. Our capacitors have also been used in mass spectroscopy chemical analysis equipment.
New applications crop up continually, and our company is always happy to assist experiments, inventors, and universities in the development of new products.
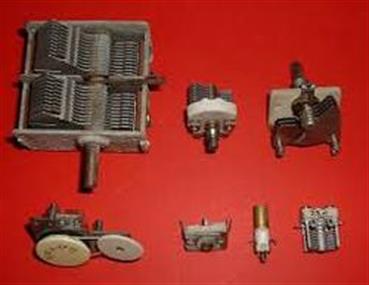
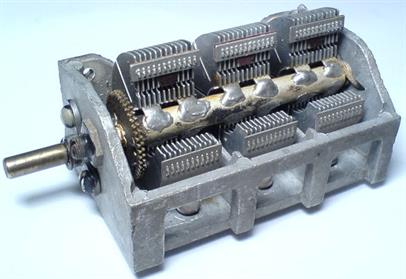
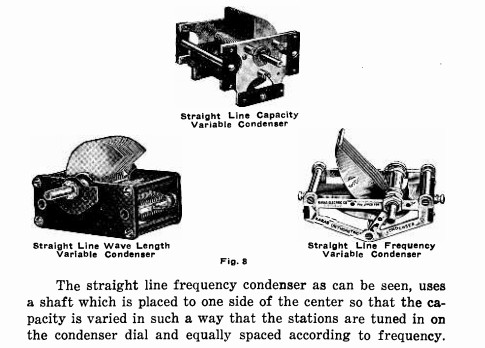
Traditional air-variable capacitors could have blades that were shaped to have a linear change in capacitance with rotation, a linear change in frequency so AM radio channels would be equally spaced with rotation, or a linear change with wavelength.